ISO Clean Room Standards and Other Classifications: Design, Redesign & Compliance
ISO Clean Room Standards and classifications are one of the most complex – yet essential – parts of designing and building a clean room. There are many important questions that need to be asked when planning for, designing and setting up your clean room. In this blog we explain how hygiene automation equipment can reduce or eliminate the risk of cross-contamination and bioburden while meeting clean room design requirements.
Types of Clean Room Classifications
Clean room Classifications follow strict clean room design guidelines from the following independent and governmental organizations:
- S. Food and Drug Administration (FDA) - CFR: Code of Federal Regulations, ex. 21 CFR Part 11
- International Organization for Standardization (ISO)
- United States Pharmacopeia (USP) – compendia of monographs
- Current Global Manufacturing Process (cGMP) Regulations
The different clean room classifications are based on contaminants which are measured in microns. Microns, or micrometers are equal to 1 millionth of a meter. For comparison, the head of a pin is 2mm.
In an effort to ensure clean room consistency, the U.S. General Service Administration published the first set of clean room standards in 1963, known as Federal Standard 209E, FS209E. These standards were accepted and implemented globally by governments and engineers until they were superseded in November 29, 2001 by ISO 14644-1. Under the International Standards Organization (ISO) three new classification standards were established in addition to standards set by FS209E, two cleaner standards and one dirtier standard. Ultimately fueled by an effort to cover more clean room environmental parameters and practices, ISO standards focus on standardizing equipment, facilities and operational methods to minimize micro contamination.
Although FED classes distinguished under FS209E have been phased out and replaced by the ISO standards, they are still widely discussed and utilized among clean room practitioners due to their familiarity and challenges associated with planning and implementing new processes and procedures.
ISO Clean Room Standards Classification Table
The comparison chart above illustrates the relationship between the two standards.
So what clean room design guidelines do you need to follow? Unclear as to which clean room classification will work for you? Check out this post outlining the top 5 answers to the most common clean room classification questions.
Top Sources of Clean Room Contamination
Bioburden is the main source of clean room contamination and is defined as the number of bacteria living on a non-sterilized surface. Over 80% of clean room contaminants are derived from the human body, with a clean room’s personnel being the primary source of bioburden.
At complete rest, individuals shed about 10,000 particles per cubic meter (cm). The outer layer of skin hosts up to a million microorganisms per square cm. Even water can introduce contaminants to the environment during the gowning process in clean rooms.
Because bioburden is the top source of clean room contamination, after determining the clean room classification and the clean room design guidelines to follow, it is essential to research the necessary equipment that will help keep your clean room contaminant-free. Clean room equipment should be designed to mitigate air, water and employee contamination.
Preventing Contamination with Effective Clean Room Design
Controlling Air Contamination:
Generally, clean rooms are designed so that the air entering a clean room is filtered to exclude dust, and other contaminants. Plus, the air inside is constantly recirculated through high-efficiency particulate air (HEPA) and/or ultra-low particulate air (ULPA) filters to remove internally generated contaminants.
Equipment used in clean room designs generate minimal air contamination. Only special mops and wipes may be used for surface cleaning, and furniture is specially designed for reduced particle emission and easy cleaning. Furthermore, materials commonly found in other environments like paper towels and cardboard which are made from natural fibers are often excluded to reduce the presence of particles. Many clean room classifications also require an air shower at the entrance to help prevent air contamination.
Controlling Staff Contamination:
Most clean room classifications require the use of an anteroom, also known as a "gray room", to create a preliminary chamber for employee sanitation to help prevent contaminants from entering the clean room. Staff enter and leave the anteroom and clean room through airlocks. Tacky mats, air showers, or both are also used to prevent contaminants from entering the anteroom and clean room from employee clothing and footwear.
Once in the anteroom, employees follow the proper gowning procedures for the clean room’s classification and put on protective clothing such as hoods, face masks, gloves, boots, and coveralls. These types of “Personal Protective Equipment”(PPE) can vary depending on the classification. Garbing order is typically dirtiest to cleanest:
- Put on shoes and/or shoe covers
- Put on facial/hair covers, glasses
- Wash hands
- Put on non-shedding gown
- Put on gloves
- Apply sanitizer to gloves –
Using proper clean room gowning methods and materials is critical to reducing contamination and providing a protective barrier between the individual and the at-risk product. Moreover, effective gowning practices protect the clean room technician from the product.
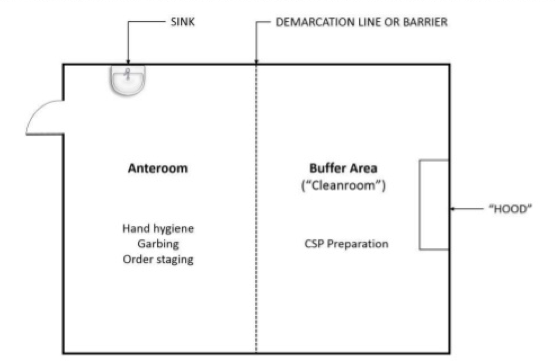
The above diagram illustrates a clean room orientation designed to reduce cross-contamination.
Meet ISO Clean Room Standards and Classification Requirements and Reduce Bioburden More Effectively with Automated Hand Washing Stations
Achieving clean room classification requirements can be challenging, yet can be quickly achieved with the right technology. Meritech’s Cleantech® Automated hand washing Stations provide the only clinically-validated and technology-based approach to employee hygiene in the world and are designed specifically to meet and exceed clean room classification requirements. In an independent study from one of our Fortune 100 medical device accounts, a 3 log reduction in measurable bioburden was proven after a single 12-second hand wash performed by our fully-automated hand washing systems.
To learn more about how Meritech automated hygiene solutions meet clean room classification requirements, reduce bioburden and improve employee hygiene practices, contact our clean room specialists at 800-932-7707.